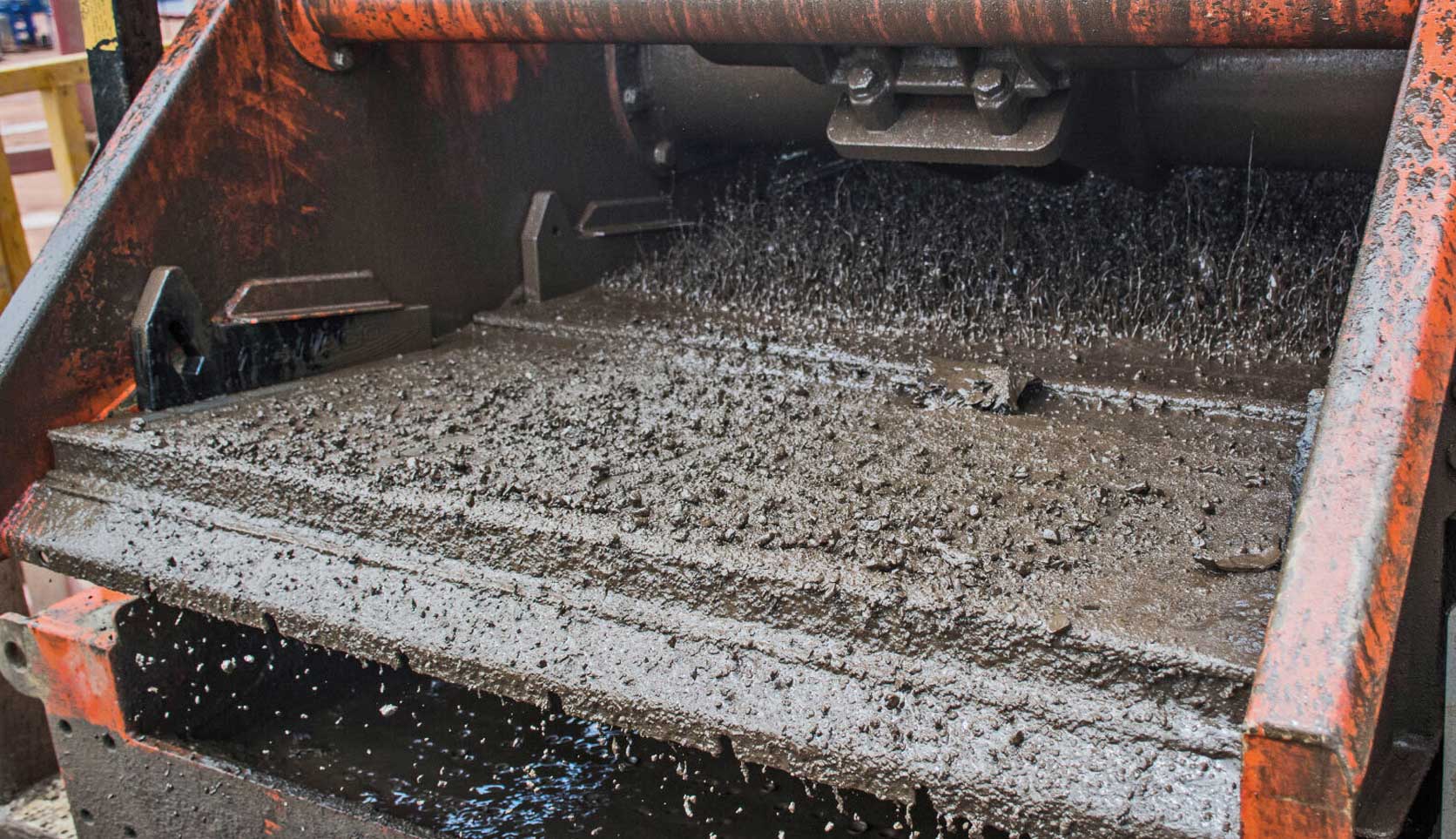
Directional Drilling Solids Control Equipment
1 - Shale Shakers
Shale shakers are a critical component of an effective solids control system. They act as the first line of defense within the system to remove larger solids from drilling fluid, allowing portions of the system located further downstream to function more efficiently and effectively on smaller particles. Essentially, when solids pass over the surface of the vibrating screen of a shale shaker, the smaller particles can pass through with the liquid. In contrast, the larger solids are separated for elimination.
Without adequately functioning shale shakers, downstream equipment such as hydrocyclones become overloaded and cannot handle the solid load. There are two types of shakers most frequently used within the Horizontal Directional Drilling HDD industry—balanced elliptical motion shakers and linear motion shakers.
2 - Shale Shaker Screens
The key component of a shale shaker is the screen. Essentially, the screen acts as a gauge that either allows or doesn't allow particles of specific sizes to pass through. Those particles small enough to pass through will do so, while others will be blocked. The surfaces of these screens are typically constructed of multi-layered woven wire screen cloth. The quality of the screen utilized by the shaker typically indicates the overall quality of the shaker itself.
Some important characteristics of the most effective screens include:
- Multi-Layered Mesh Screens: Multi-layered mesh screens consist of at least two screen cloths, typically made of different types of mesh, which are mounted on a single screen panel, as illustrated in Figure Five. The openings of these screens can vary significantly in both shape and size, with the mesh being defined by the number of openings per linear inch. To effectively measure the mesh, begin at the center of one wire and count the number of openings between that point and an endpoint one inch further.
- Tensioned Stainless Steel Wire Mesh: It is important that wire mesh utilized in a shaker screen be resistant to corrosion and that it fits properly to provide a taut stretched upper surface to avoid damage to the equipment and poor solids cuts.
- API Qualification: Since the quality of screens varies significantly, it is essential to rely upon API qualifications to determine whether a screen meets internationally acceptable standards. Only API 13C-qualified screens should be implemented in the system to ensure an effective screen.
Always consider the overall configuration of your solids control system before choosing which screens will be the best fit in terms of efficiency and effectiveness. For example, if a system utilizes a scalping system and fine screen system, then the scalping screens must be sized appropriately to avoid drilling fluid sheeting off from the shaker, which is referred to as whole mud losses. If the scalping screen is too fine, little to none of the drilling fluid will pass into the "dirty tank" of the solids control system, limiting the value of the system. The screens must be considered not only at the start of the project but continuously as the screen required will be relative to the subsurface conditions. In fact, based on differences in drilling length and depth, several different screen combinations may be necessary for effective solids control.
Additionally, it is important to keep in mind that the size of the screen openings—or the distance between wires in the screen cloth—is measured in fractions of an inch or microns. Screens of the same mesh can still have various sized openings based on the diameter of the wire utilized on the screen. Wires with smaller diameters will yield larger screen openings, permitting larger particles to pass through, whereas wires with larger diameters allow smaller particles through. This is why it is essential to remember that the size of the opening in a screen, rather than the mesh count, dictates the size of the particles the screen will permit through. Because of these details, HDD system users should always be sure to rely upon API 13C designations to compare screens. This ensures that proper selection can be completed for each job and better guarantees the screens offer performance continuity and are more easily compared from operation to operation.
3 - Shale Shaker Maintenance
To achieve a high level of efficiency, fine mesh screen shakers must be utilized. However, this necessitates specific care and maintenance to ensure continuous performance. The most critical care requirements of fine mesh screen shakers include:
- Regular Power Washing: Screens must be washed down frequently using a power washer. While it is important for all projects, it is critical when drilling occurs in locations that are made up of highly reactive or "sticky" solids, such as clay, or when drilling with fluids that utilize polymers.
- Checking for Damage: It is critical that screens are regularly assessed for rips or tears and that any holes are plugged. The screens should be checked frequently because holes can lead to significant mud weight problems.
- Properly Mounting Screens: Always ensure that screens are mounted correctly to help mitigate solids bypass. Since most shakers rely on relatively simple wedge-block installation systems, it should be confirmed that wedges are tightly installed, and the screens fit snugly. Additionally, it is critical to ensure that the screens are "seated" correctly so that all seals are fully engaged with the shaker.
- Properly Angling the Shaker: It is important to ensure the shaker is placed at the proper angle. Of course, the shaker inclination must be carefully considered based on the volume of solids entering the system. Further, always confirm that the shaker is operating perfectly level, regardless of the rig position.
- Checking Electrical Wiring: Regularly check all electrical wiring to ensure wiring insulation remains intact. Keep in mind that High G shakers tend to wear through wiring insulation. These systems are exposed to very wet conditions, leading to electrical safety issues if not carefully monitored.
- Ensuring Proper Lubrication of Equipment: It is essential to properly lubricate equipment, including vibrator motors, pump motors, and leveling jacks. These are precision devices, and they require regular preventative maintenance. Refer to the original manufacturer's manual, which provides clear instructions on the minimum preventative maintenance needed to ensure maximum equipment life and functionality.
- Checking for Plugged Screens: In addition to the above, frequent checks should be made for any plugging of the fluid on screens. To mitigate this issue, the shaker angle can be increased or decreased. Or, a different screen—either more course or finer—may need to be installed to solve the issue.
In completing the above steps, it is critical to remember that the shale shaker is the first step in your solids control system. As the first line of defense, it should be well maintained. To ensure effective and efficient ongoing performance, all rig personnel should understand what constitutes proper operation and maintenance of the shale shaker.
4 – Hydrocyclones
Designed to make the settling process occur more quickly, hydrocyclones are simple mechanical devices with no moving parts. Hydrocyclones rely on pressure transforming into centrifugal force to speed up particle settling. The process works in accordance with Stoke's Law, and essentially the device generates a settling pit under controlled conditions that lead to the rapid settling of solids. These easy-to-maintain devices can remove particles down to 25 microns, much smaller than the particles the finest mesh screens can handle.
Hydrocyclones include a conical shell with a single small opening at the bottom to allow underflow discharge. They also have a larger opening at the top, which allows for liquid discharge through an internal "vortex finder" and a feed nozzle on the side of the device. When drilling mud enters the cyclone under pressure from the centrifugal feed pump, the velocity of the mud leads to rapid rotation within the main chamber. If you've ever created a "tornado in a bottle," you've seen this in action. Then, lightweight, fine solids and liquid mud spiral in and up to be discharged through the liquid outlet, while heavier, more coarse solids move outward and down to be released through the solid outlet.
While the design features of hydrocyclones vary significantly across the industry—often based on size—the most typical HDD cyclones are crafted of composite materials such as polyurethane. They are generally quite strong and hold up well to wear and tear during the drilled process. However, it is important to note that some drilling conditions may favor ceramic cone inserts as these can slow equipment erosion by abrasive solids.
There is a great deal of variation in the size of hydrocyclones, ranging from twelve inches to just two. The most commonly used cyclone sizes are four, five, ten, or twelve inches. These measurements refer to the innermost diameter of the largest cylinder section of the device. Typically, the larger the cone, the larger the cut point and throughput. However, keep in mind this is not always the case. Refer to Table Seven for a relative performance comparison between hydrocyclones, but remember that the cone performance will vary from manufacturer to manufacturer.
Utilizing several hydrocyclones parallel to one another can provide enough capacity to handle the volume circulating within the system while also providing some reserve. This is known as manifolding, and it can be done in a vertical position or nearly horizontal, depending on the system design parameters and what is most convenient for the specific project. The position does not ultimately have any impact on the system's performance. However, the internal geometry of the cyclone does have a significant impact on operating efficiency. In particular, the length and angle of the conical section and the size and adjustment are critical components of ensuring the effective separation of solids from the load.
There are several different ways to measure the operating efficiency of hydrocyclones. Each must factor in the ability of the system to remove the maximum amount of abrasive solids while ensuring minimum loss of fluid.
4.1 – Desanders
Not critical to every application, desanders are, essentially, larger hydrocyclones. With a diameter of 5 inches or more, desanders are located downstream from the shale shaker but before the desilter—assuming that component is included in the system. Like their names, the desander's role is to remove sand-sized particles and larger drilled solids that have made it past the shale shaker. Together with some liquid, these materials are removed and discarded from the system into the waste tank, while clean mud continues to the next tank in preparation for the desilters.
To ensure the effective operation of desanders in your solids removal system, it is helpful to consider the following:
- Sizing: It is important to size the desander appropriately. It should have the capacity to process 100-125% of the total mud load. This allows it to accommodate any additional volume associated with cuttings, particularly when utilizing very coarse screens.
- Minimizing Frictional Losses: It is important to maintain short, straight lines with as few pipe fittings as possible to reduce pressure loss on the feed line and keep backpressure on the overflow discharge line to a minimum. Additionally, never reduce the diameter of the overflow line from that of the overflow discharge manifold.
- Directing the Overflow Discharge Line: Always be sure the overflow line is directed downward to the next phase of the system downstream at an approximately 45-degree angle. The efficiency of the cyclones is reduced when the overflow discharge line is installed in a vertical position as it may lead to a vacuum on the discharge header that pulls solids through the cyclone overflow. This is easily avoided by ensuring the end of the discharge line remains above the surface of the mud.
- Installing an Equalization Line: Install a low equalizer line to allow any backflow to enter into the desander area.
While most desanders are relatively uncomplicated devices, here are a few fundamental principles to keep in mind to ensure they can operate at peak efficiency:
- Operating Pressure: The recommended feed manifold pressure is typically around 30 PSI to ensure efficiency with low wear and tear on the system.
- Cone Inspection: Regular monitoring of the cone's discharge orifice is important to ensure it is not plugged. Desander maintenance is not overly complicated and typically only involves flushing out the feed manifold between bores to ensure nothing large has collected there that could cause cone plugging—and inspecting the cone for excessive wear. By remaining committed to a preventative maintenance routine, downtime is decreased. It is much easier to perform repairs between bores than during a drilling operation.
- Recirculation: You should aim to continuously run the desander, allowing the fluid overflow to re-process again and again. While many systems available only allow one pass through the desanders, this is inefficient and does not allow for a proper cut. Only the desander overflow should be permitted to the next phase.
- Spray vs. Rope Discharge: To achieve the best possible efficiency, operating the desander using a light spray over a heavier rope discharge is vital.
4.2 – Desilters
Desilters utilize smaller hydrocyclones—typically 5 inches or smaller—to allow for the elimination of the finest particle sizes of any solids removal equipment. A desilter uses smaller hydrocyclones, usually 5 inches or smaller, to remove particles of 25 microns or larger. Typically, several cones are utilized to achieve the capacity necessary for the system's load. It is essential to keep the following in mind when installing a desilter:
- Sizing: It is important to size the desilter appropriately. It should have the capacity to process 100-125% of the total mud load.
- Arranging the Flow: The desilter should take suction from the compartment receiving the fluid that the desander has already processed.
- Minimizing Frictional Losses: It is important to maintain short, straight lines using as few pipe fittings as possible to reduce the loss of pressure on the feed line and keep backpressure on the overflow discharge line to a minimum. Additionally, never reduce the diameter of the overflow line from that of the overflow discharge manifold.
- Feeding the Pumps: Do not use the same centrifugal pump to feed both the desander and the desilter. Should you need to operate both pieces of equipment simultaneously, they can be installed in a series, each with a separate pump.
- Directing the Overflow Discharge Line: Always be sure the overflow line is directed downward to the next phase of the system downstream at an approximately 45-degree angle. The efficiency of the cyclones is reduced when the overflow discharge line is installed in a vertical position as it may lead to a vacuum on the discharge header that pulls solids through the cyclone overflow. This is easily avoided by ensuring the end of the discharge line remains above the surface of the mud.
- Installing the Equalization Line: It is necessary to install a low equalizer line that will allow for backflow into the desander.
- Pretreating the Inlet: Assuming a shaker scalping cut is not taken before the material reaches the hydrocyclones, installing a guard screen over the suction with quarter-inch slots is necessary. Doing so will stop large trash from entering the unit, which could plug the cones. There should always be some form of scalp cut before the desilters to eliminate large, coarse solids from the flow.
The entire system's efficiency is improved by operating a desander ahead of the desilter, as it takes a significant load off the desilter. Essentially, operating both at peak efficiency is similar—but there are a few things to keep in mind to achieve maximum effectiveness:
- Operating Pressure: The recommended pressure for optimum desilter functioning is typically 32-40 PSI.
- Apex Adjustment: The cone apex can be adjusted to be slightly open to assist in achieving more effective solids removal.
- Cone Inspection: It is important to inspect the cones regularly to ensure no bottom plugging or flooding occurs. A plugged cone can allow solids to return to the active mud system, sacrificing efficiency. Should you find a plug in the cone, it can typically be unplugged using a long, thin rod. If you notice a cone flooding, you may need to unblock a portion of the feed that has become blocked or adjust the cone. First, inspect the cone to ensure it isn't simply worn out and needs to be replaced. More often than not, it will be plugged as a desilter's smaller cyclones are more likely to become overwhelmed with larger solids than a desander's. This highlights the importance of an active plan of inspecting for wear and plugging between bores—unless a failure occurs, in which case it must be done immediately. It should also be inspected often to ensure the cone is not worn out. A desilter's smaller cyclones are more likely than a desander's cones to become plugged with oversized solids, so it is crucial to inspect them often for wear and clogs. Additionally, the feed manifold should be flushed and checked for debris as part of a regular maintenance plan between bored.
- Recirculation: You should run the desilter continuously, allowing the fluid to overflow back into the system and repeat the process repeatedly.
4.3 - Centrifugal Pumps
In addition to the aforementioned components, another critical part of an efficient, high-quality solids control system is the inclusion of centrifugal pumps. Not only do centrifugal pumps mix up the mud to be pumped down the borehole, but they also generate feed pressure and volume necessary for the operation of the hydrocyclones. Following a regular maintenance program is critical to the successful ongoing operation of the pumps themselves and the other solids control equipment in your system. The following is a list of proper maintenance procedures.
- Alignment: Always confirm that the motor and pump alignment is correct before operating the pump.
- Bearings: Be sure to inspect the mechanical end of the pump to ensure it is adequately lubricated with bearing oil or grease.
- Packing: The gland packing must not be overly tight. You should check for proper adjustment and follow the manufacturer's recommendations to grease the gland packing.
Employing a solid maintenance plan for your pumps is important, as about 50% of your regular maintenance in connection with your mud system will be on the pumps. This is not surprising, given that abrasive solids consistently wear away at impellers and seals. Still, it highlights the importance of careful monitoring and operating the pumps only within their performance limitations. Pumps being used close to or beyond operational limits will require more maintenance and likely have a shorter lifespan than those operated well within their performance constraints.
Discussions with the original equipment manufacturer can ensure that the pumps are properly set up for your specific operation and appropriately sized to achieve the application's needs in terms of mud weight, solids content, and viscosity.
4.4 – Centrifuge Technology
Centrifuge technology is relatively new to the HDD industry. While they are expensive compared to shakers and hydrocyclones, they can have a notable impact on the overall quality of your system. Figures Two and Four show that centrifuges can target ultra-fine and colloidal solids that shakers and hydrocyclones cannot. In fact, depending on the speed the centrifuge is operating at, operators can even target solids of a specific size. However, clays such as bentonite are made up of solids of less than five microns, which is outside the capabilities of a centrifuge. The centrifuge must operate at its maximum speed capability to successfully separate solids in the two- to five-micron range.
A primary system—or using shakers and/or hydrocyclones as pretreatment—must be deployed in cooperation with the centrifuge. To succeed with the centrifuge, the mud must first go through these phases. Still, even with the need for pretreatment and the high level of sensitivity, operators have been able to quadruple the lifespan of their drilling fluid. This can generate significant cost savings on waste disposal expenses.
In addition to these manual removal options, a closed-loops solids control system can also rely upon chemically enhanced measures to remove 100% of suspended solids from the drilling fluid. By adding a polymer, a closed-loop solids control system can accomplish this. This method is the only option within the HDD industry that will allow for the complete recycling of the drilling fluid. However, as the costs of disposal rise and environmental regulations become more complex, centrifuge technology is likely to become the standard HDD technology.